Rising damp treatment
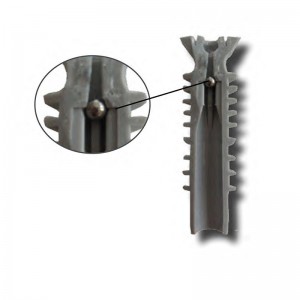
Injector 12 mm without head grey x1000
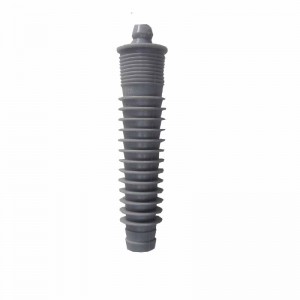
Injector 12 mm with head L65 grey per 1000
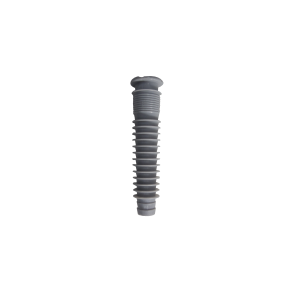
Flat head packer Ø12 grey

Injector Ø14 with head per 1000
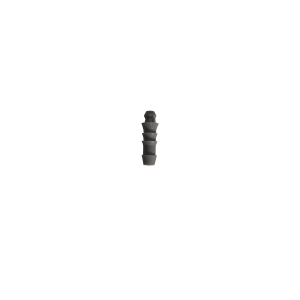
Injector 6,5 with head grey per 1000

Flat head packer ø6.5 grey per 1000
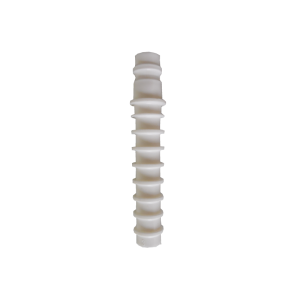
Cement Injector white per 1000
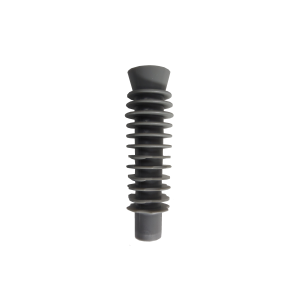
Inj 18 monobloc grey x500
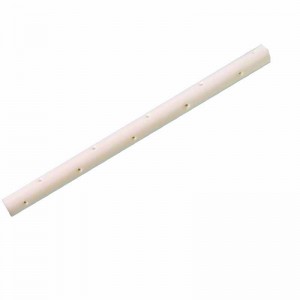
Diffusing tube for inj. 12 L 2m
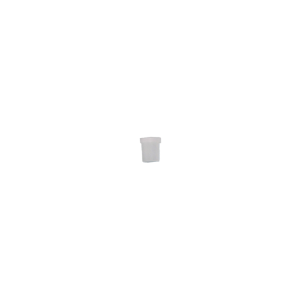
Caps for Diffusing tube 12mm
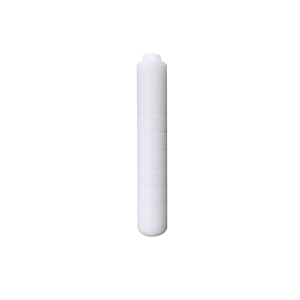
Female mounting tool for injectors with head...
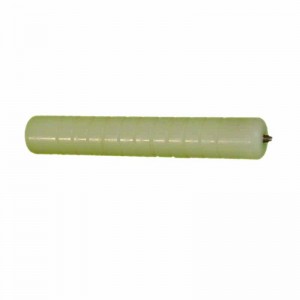
Male mounting tool for injectors without head ø 6.5-9.5-12
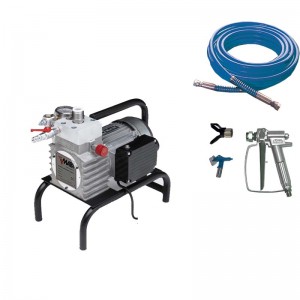
MABI Airless diaphragm pump 4.5L in set
Rising damp treatment method by injection
Drill
To prepare the rising damp treatment, all coatings have to be removed; and brittle or non-adhesive parts located into the injection zone have to be brushed.
If the walls have many cavities or voids, prefilling these parts with a suitable non-shrinkable filler before the damp proof course injection is needed.
The injection holes have to be drilled on the outside, following a horizontal line or are placed in a staggered row in order to create a double chemical barrier.
Drilling is about 10cm above ground, in the mortar beds, spacing between boreholes is about 10/15cm and 2/3rd of the wall thickness.
Drill bits are available here
Injection packers' implementation
Plastic injection-packers are inserted into each injection hole, using a hammer and a mounting tool. The packers have been developed to keep enough pressure during and after the injection; to obtain an optimal diffusion of the damp proof course chemical into the thickness of the wall. It’s recommended to use diffusing tubes with the packers. Diffusing tubes have 360° micro holes, are driven into the thickness of the wall and adapt themselves at the bottom of the packer.
Inject
The damp proofing product is injected with low pressure thanks to a gun and the corresponding MABI pump.
With their inner valve system, the Mabi injectors will force the waterproofing liquid solution to spread inside the masonry with no leaks or splash back.
For each injection, the injected product quantity should be controlled in order to respect the manufacturer’s chemical product instructions (DPC solution quantity to be injected per linear meter).
The packers allow an injection into the wall without backflow of chemical from the injected hole or the adjacent bore holes.
Renovate
The product reacts in the masonry to become hydrophobic resin and create a barrier, called a remedial damp proof course (DPC).
After 2-3 weeks the moisture flow is stopped by the chemical barrier. It is then necessary to facilitate at the maximum the drain conditions of the treated masonry (aerate, warm up and dehumidify). Regular monitoring of humidity can follow the progress of drying and renovations begin only when the wall reaches a humidity level inferior to 5%.
Combine this approved method with a Damp Proof Course chemical, for example PCI Bohrlochsperre, Schomburg Aquafin-F , Remmers Kiesol, Bornit SI, Botazit MS10, Kreisel 900, Mapei Mapestop, Mautrol 1K, Sopro VK 690, Weber.tec 940 or any other brand labelled for this application in your country.